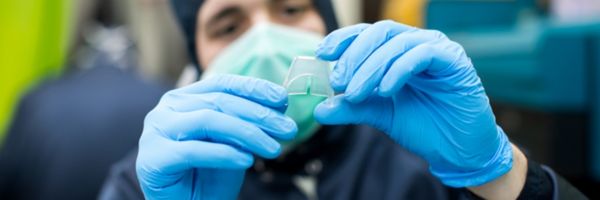
Shelf-life testing is a critical step in preparing a medical device for the market and is mandatory for all products. Fail to perform this testing correctly and you will likely have to recall products, and risk significant damage to your market profile.
Medical device shelf-life testing should be carried out in accordance with BS EN ISO 11607-1:2020. This ISO standard gives the guidance for choice of packaging material used and their required performance. There are other standards linked to this publication which should be consulted where relevant.
Shelf-life testing for new and existing medical devices
Shelf-life testing for medical devices is focused on the performance of the device and the performance of the product packaging over time, that is, how long the packaging keeps the product sterile, and how long the device performs to specification.
For established medical devices, shelf-life testing can be based on existing performance data. However, for new products, there is no existing data on which to base testing and this represents a challenge for manufacturers who wish to launch new products to market quickly.
To overcome this challenge, manufacturers are allowed to use simulated test data and real-time test data in parallel. However if the device has multiple parts, the part with the lowest known shelf life determines the overall shelf life.
Types of shelf-life testing for medical devices
There are two key types of shelf-life testing for medical devices: real-time ageing and accelerated ageing. The latter plays a key role in shelf-life testing for new medical devices.
- Real-time ageing: this is shelf-life testing of medical devices in real time. A day-zero test is carried out to provide baseline performance data and, thereafter, the device is tested at key points and compared to that initial data. Keep in mind, product performance can improve over time – it would be wrong to presume that a product will always degrade.
- Accelerated ageing: this requires specialist equipment and expertise. As a result, it is often outsourced. A device is placed in a temperature and humidity-controlled ageing oven, which simulates conditions in which one month roughly equals one year. Full boxes of product are placed in the oven, and a full box will be removed at each time point. Once all time points and tests have been completed, the data can be trended and compared to the day 0 results. If all tests pass as expected, the product can be cold with the estimated shelf life. The Real time data as it is gathered, will always take priority and must be performed in tandem.
The logic behind the framework of the shelf-life testing is based on both accuracy and efficiency. If a device passes the test after year one and year two but fails at year three, you can choose to apply a two-year shelf life. If the same device were only tested after three years, it would register a fail and the testing procedure would have to be repeated, costing time and money.
Benefits of outsourcing medical device shelf-life testing
Failure to carry out shelf-life testing is most commonly identified when a device is audited. At this point, the device is already on the market. As a result, it may have to be withdrawn and tested or re-tested. This takes at least three to six months, during which time sales are lost and significant admin and testing costs are accrued.
Outsourcing shelf-life testing is a safeguard against this failure and the costs that it incurs. Using a specialist partner has a range of performance and cost-efficiency-related benefits. Aside from ensuring that your device stays on the market, outsourcing shelf-life testing means that you don’t need to invest in the acquisition, maintenance, operation and storage of testing equipment.
Additionally, the existing product data to which an outsourcing partner has access is critical. Their expertise and experience should allow them to use this information to provide optimal initial data on your device and create a highly accurate estimate of its shelf life, giving you the clearest possible picture of timelines as you plan to go to market.
Meridian Medical is an established and experienced contract medical equipment manufacturer specialising in a wide range of medical device design, development and supply services.
To find out more about how Meridian Medical can help you with your medical product design and manufacture, get in touch today by filling out our online form or contacting us on 01903 732344 or info@meridian-medical.com.
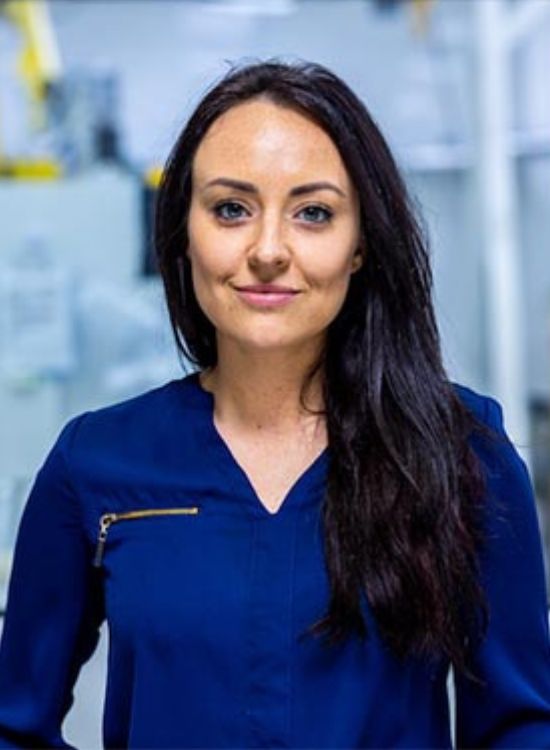
Author: Fiona Chitty, Quality and Process Engineer
Fiona Chitty brings a fresh perspective to Meridian Medical, where she has spent the past four years honing her expertise in quality and process engineering. With a Bachelor of Science in Physics and a Bachelor of Engineering in Chemical Engineering, Fiona is deeply involved in root cause investigations, complaint resolution, trend analysis, and continuous process improvement. Her role is critical in maintaining high standards across all departments, ensuring the delivery of top-quality medical devices. Fiona’s passion for problem-solving and her analytical approach make her an invaluable asset to the team.