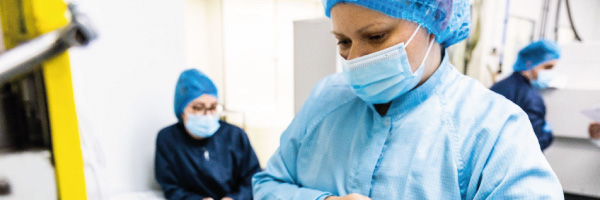
In the fast-paced world of medical device manufacturing, efficiency, precision and cost-effectiveness are paramount. Among the manufacturing techniques that rise to meet these challenges, injection moulding stands out. This versatile and highly efficient process has not only become a cornerstone in the production of medical devices but also offers a host of other benefits. This blog aims to explore the advantages of injection moulding, and how this technique has revolutionised the medical device industry
1. Precision and Consistency
Injection moulding is uniquely positioned to meet the stringent demands for precision and consistency within the medical device industry. The process involves injecting molten material – often specialised medical-grade polymers – into a custom-designed mould under high pressure. This technique ensures that every component is shaped exactly as intended, down to the micron level. In a sector where minuscule deviations can have significant implications for patient care and treatment outcomes, the exacting nature of injection moulding proves invaluable. For manufacturers, this translates into fewer defects and reduced costs associated with quality control, further emphasising the advantages of injection moulding.
2. Cost-Effectiveness and Benefits
In medical device manufacturing, cost-effectiveness is not merely an advantage, it’s a necessity. Injection moulding stands out by offering a myriad of financial benefits over traditional manufacturing methods such as machining or casting. This process allows for the creation of multiple components in a single cycle, substantially increasing throughput. Moreover, the high efficiency of injection moulding minimises waste material, further contributing to cost savings. Another significant benefit is the reduced need for post-processing, often eliminating the need for additional finishing, thus saving time and labour costs. All these factors combine to create a cost-effective production ecosystem that benefits not just manufacturers but ultimately contributes to more affordable healthcare solutions for end-users.
3. Shorter Production Time
In the healthcare sector, where timely intervention can be a matter of life or death, the speed of production in medical device manufacturing takes on heightened importance. Injection moulding is particularly advantageous in this regard. The process boasts rapid cycle times, often as quick as a few seconds, which facilitates accelerated production schedules. This expediency isn’t just about speed for its own sake; it’s about how quickly medical devices can transition from manufacturing to market. Quicker market entry means the ability to meet immediate medical needs more effectively, thereby solidifying the advantages of injection moulding in producing essential healthcare equipment.
4. Customisation and Flexibility
The unique and highly specific demands of healthcare applications require a manufacturing process that allows for a high degree of customisation and flexibility. In this context, injection moulding excels. Not only does it allow for the production of complex geometries and internal structures, but the moulds themselves can be customised to incorporate features like engravings or identifiers, essential for traceability in medical devices. Manufacturers also have the flexibility to adjust various parameters, from material composition to temperature controls, allowing the tailoring of products to meet stringent sterility and biocompatibility requirements. Furthermore, advancements in technology enable the use of multi-cavity moulds, facilitating the simultaneous production of multiple components with varying designs. These capabilities underscore the advantages of injection moulding and its suitability for producing highly specialised medical equipment.
5. Material Diversity
In the domain of medical device manufacturing, the selection of materials holds particular significance due to direct or indirect contact with the human body. Injection moulding rises to the challenge by offering compatibility with a myriad of medical-grade materials. These range from biocompatible polymers and thermoplastics to silicone and high-performance resins. Such material diversity provides the flexibility to meet not only sterility and biocompatibility requirements but also offers scope for customising mechanical properties like strength and flexibility. This adaptability underlines yet another advantage of injection moulding, making it an ideal choice for a plethora of healthcare applications
6. Enhanced Quality Control
Stringent quality control isn’t just a regulatory requirement; it’s a moral obligation. One of the most compelling advantages of injection moulding lies in its inherent capability to offer granular control over each step of the production process. From the input material quality to the precision of the mould and the calibration of injection parameters, every element can be rigorously monitored. Furthermore, state-of-the-art injection moulding machines are equipped with advanced sensor technology and real-time feedback systems. These systems not only facilitate immediate adjustments to ensure optimal performance but also allow for statistical quality control, thereby significantly reducing the risk of defects and waste. Such meticulous quality assurance mechanisms make injection moulding an ideal choice for the exacting standards required in medical device production.
7. Scalability
Scalability is often a make-or-break factor for success. One of the advantages of injection moulding that truly sets it apart is its capacity for effortless scalability. Whether the requirement is for a limited series of prototypes or a full-scale production run, the process is designed to adapt seamlessly. Modular mould designs allow for straightforward adjustments, enabling manufacturers to easily switch from low to high-volume production without extensive retooling. Moreover, automated systems and process optimisation techniques further streamline scalability, allowing for rapid adjustments to meet fluctuating market demands or regulatory requirements. This flexibility in production volumes not only saves time but also optimises operational costs, exemplifying why injection moulding is so effective and versatile in addressing the varied needs of the medical device sector.
Medical Applications
Injection moulding’s unique attributes make it a preferred choice for a wide array of applications. From disposable items like syringes and catheters to more complex, life-saving devices like heart valves and surgical robots, the technique is invaluable. The advantages of injection moulding come to the fore when one considers the stringent sterility requirements and material compatibility needed in these devices. Advanced moulding techniques even allow for the incorporation of antimicrobial agents directly into the mould, offering an additional layer of patient safety.
In conclusion
From intricate designs to customisable solutions, the advantages of injection moulding in medical device manufacturing are hard to ignore. As medical technology continues to evolve, this method will undoubtedly play a central role in producing innovative devices that improve patient outcomes and contribute to advancements in healthcare globally.
Meridian Medical is an established and experienced contract medical device manufacturer specialising in a wide range of medical devices. We offer design, regulatory assistance, cleanroom injection moulding, cleanroom assembly, contact packaging and sterilisation Management. We have over 30 years’ experience supplying UK and European companies.
To find out more about how Meridian Medical can help you with your medical device manufacture, get in touch today by filling out our online form or contacting us on 01903 732344 or info@meridian-medical.com.
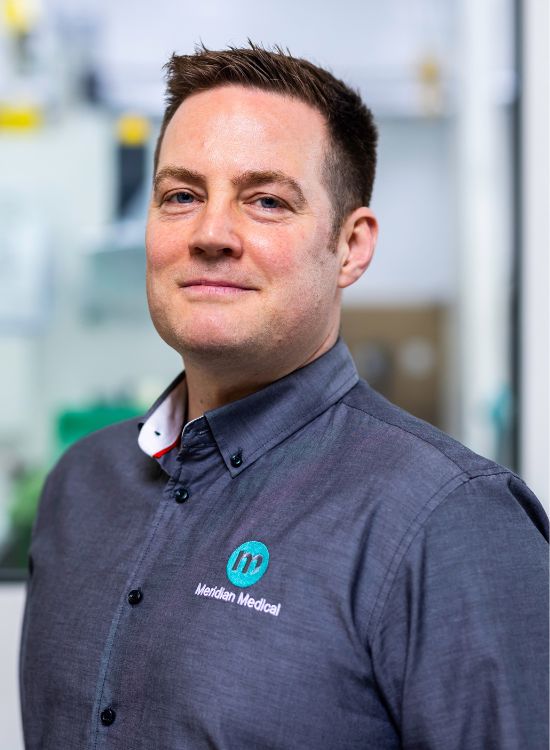
Author: James Fenton, Managing Director
James Fenton, Managing Director of Meridian Medical since 2017, has over 20 years of industry experience. He has been pivotal in developing and producing over 500 types of single-use medical devices, including CE-marked class 2 and 3 devices. With a strong focus on business strategy, project management and customer support, James ensures Meridian Medical's agility and innovation. His expertise is backed by qualifications in Business Studies and Medical Process and Equipment Validation, plus extensive industry training. James's insights into the industry that he has dedicated his entire career to provide a bank of invaluable information aimed at increasing knowledge of and driving advancements in medical device manufacturing.