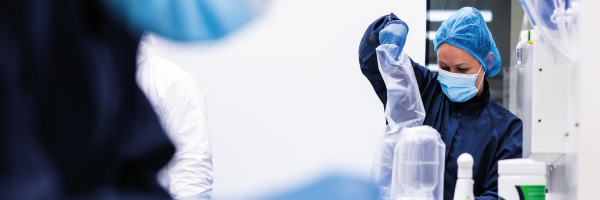
Injection moulding is a widely adopted manufacturing process in the production of medical devices. While it offers numerous advantages, including precision and scalability, the cost of injection moulding can vary based on many factors. Understanding these influencing factors is essential for medical device designers and manufacturers to optimise their production processes and deliver cost-effective solutions without compromising on quality. In this blog, we delve into the key factors that impact the cost of injection moulding for medical devices.
- Complexity of Design:
The complexity of the medical device design is a crucial factor influencing the cost of injection moulding. Devices with intricate geometries, tight tolerances, and multi-component assemblies may require multiple specialised moulds and production techniques, leading to higher upfront tooling costs and longer production times. Simplifying the design without compromising functionality can help reduce manufacturing expenses.
- Material Selection:
The choice of material significantly impacts the overall cost of injection moulding. Medical-grade materials, especially biocompatible polymers and high-performance thermoplastics, are typically more expensive than standard plastics. The material’s properties, such as strength, flexibility, and biocompatibility, must align with the intended medical application, but selecting cost-effective alternatives can help manage production expenses.
- Volume of Production:
The volume of medical devices to be manufactured directly affects the cost per unit. Injection moulding is well-suited for high-volume production due to its efficiency in creating multiple components in a single cycle. Economies of scale come into play, with larger production runs often leading to reduced per-unit costs. For lower production volumes, manufacturers must carefully balance cost considerations with the required quality standards.
- Tooling and Equipment:
The cost of mould tooling and equipment is a significant initial investment in injection moulding. Custom-designed moulds are essential to replicate the device components accurately. The complexity and size of the mould, as well as the number of cavities, influence the tooling cost. Manufacturers can explore the use of multi-cavity moulds or consider leasing options to optimise tooling expenses.
- Post-Processing and Finishing:
Post-processing steps, such as trimming, assembly, and surface finishing, impact the final cost of injection moulding. Complex assembly requirements or additional finishing processes, like polishing or coating, add to the overall manufacturing expenses. Optimising these steps through automation and efficient assembly techniques can help manage costs.
- Quality and Regulatory Compliance:
Medical devices must meet strict quality and regulatory standards to ensure patient safety. Compliance with ISO and FDA regulations often involves additional testing, validation, and documentation, which can contribute to the overall cost. Investing in quality control and regulatory compliance is crucial to producing safe and reliable medical devices.
- Supplier Relationships:
The choice of suppliers, both for materials and injection moulding services, can influence cost. Establishing long-term relationships with reliable suppliers can lead to more competitive pricing and improved efficiency in the production process.
As the demand for medical devices continues to grow, manufacturers must consider various factors that influence the cost of injection moulding. A holistic approach to design, material selection, production volume, tooling, post-processing, and supplier relationships is essential to strike a balance between cost-effectiveness and product quality. By understanding and optimising these influencing factors, medical device manufacturers can deliver innovative, safe, and affordable solutions that benefit healthcare providers and patients alike
Meridian Medical is an established and experienced contract medical device manufacturer specialising in a wide range of medical devices. We offer design, regulatory assistance, cleanroom injection moulding, cleanroom assembly, contact packaging and sterilisation Management. We have over 30 years’ experience supplying UK and European companies.
To find out more about how Meridian Medical can help you with your medical device manufacture, get in touch today by filling out our online form or contacting us on 01903 732344 or info@meridian-medical.com.
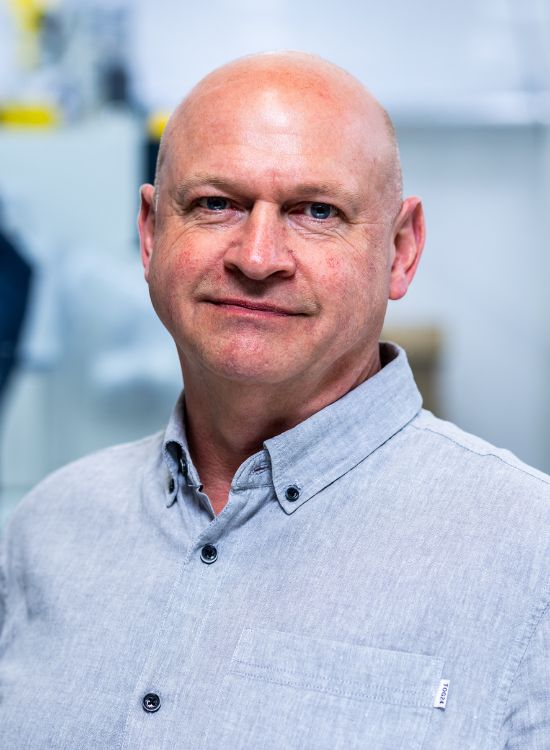
Author: Paul Kearsley,
Technical Manager, Meridian Medical
Paul Kearsley brings a lifetime of engineering expertise to his role as Technical Manager at Meridian Medical. With an HNC in Mechanical Engineering and a foundation built during a four-year engineering apprenticeship, Paul has spent over 40 years running his own design company. Over the decades, he has designed more than 1,000 consumer, industrial, and medical devices, showcasing his ability to deliver innovative solutions across a broad spectrum of industries.
A pioneer in the transition from traditional drafting techniques to modern CAD workflows, Paul began his career on the drawing board, adopted AutoCAD 2D early on, and embraced 3D modelling with SolidWorks in 1997. His vast experience and technical leadership play a key role in Meridian Medical’s commitment to producing high-quality, single-use medical devices.