Quality control – a Meridian Medical Guide to Medical Device Manufacturing
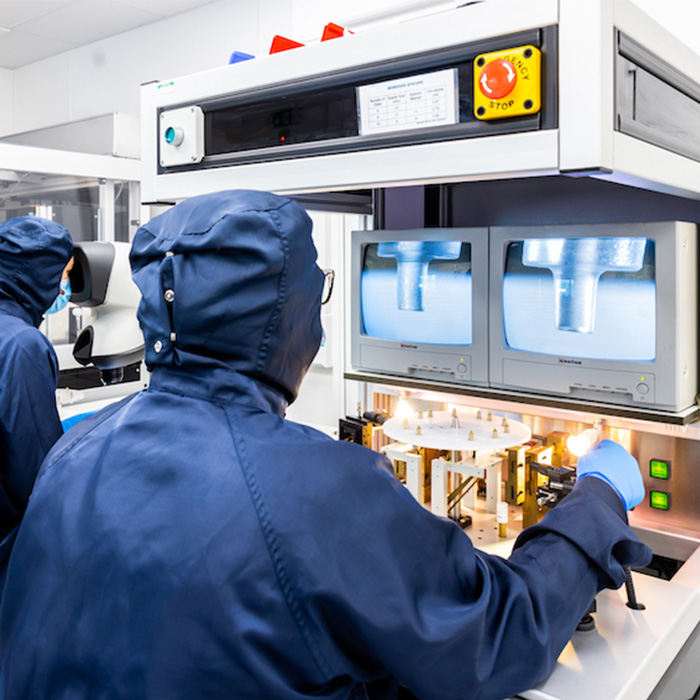
GUIDE
In this blog post, we provide a comprehensive guide to medical device manufacturing quality control, covering the key steps involved in the process.
Remember, the manufacturer is the entity legally responsible for the certification of the device. This is not necessarily the contract medical device manufacturer or company that assembles the device.
Step 1: Design controls
The first step in medical device manufacturing quality control is design control. Design control ensures that a device’s design is appropriate for the intended use, and the device meets the user’s needs. The process involves the following steps:
1.1 Design and development planning: The manufacturer should plan and document the design and development process, including design inputs, outputs, reviews, and verification and validation (also known as V&V) activities.
1.2 Design input: The manufacturer should document the device requirements based on the user’s needs and expectations. You can refer to the safety and performance requirement checklist for a comprehensive list of requirements (click here for Sven Piechottka’s free template).
1.3 Design output: The manufacturer should document the design specifications and ensure that they meet the design input requirements.
1.4 Design review: The manufacturer should conduct a formal design review to evaluate the design’s suitability, identify any issues, and ensure that the design meets the intended use.
1.5 Design verification: The manufacturer should verify that the design meets the design output requirements.
1.6 Design validation: The manufacturer should validate the design to ensure that it meets the user’s needs and intended use.
Step 2: Production controls
Production controls ensure that the medical devices are manufactured consistently and meet the quality standards. The process involves the following steps:
2.1 Document control: The manufacturer should establish and maintain procedures for document control to ensure that all documents related to the manufacturing process are up-to-date and accurately reflect the processes followed.
2.2 Equipment control: The manufacturer should ensure that all equipment used in the manufacturing process is calibrated, maintained and validated to ensure its accuracy and reliability and suitability to the assembly process.
2.3 Process control: The manufacturer should establish and maintain procedures for process control to ensure that the manufacturing process is controlled and monitored to produce devices that meet the required quality standards.
2.4 Inspection and testing: The manufacturer should establish and maintain procedures for inspection and testing to ensure that the devices meet the design specifications and required quality standards.
2.5 Packaging and labelling: The manufacturer should ensure that the devices are appropriately packaged and labelled, with all necessary information and instructions for use. This will be a significant amount of work. Having the correct type of packaging to ensure the device arrives with the end user in perfect condition will require a number of different tests.
Step 3: Process validation
Process validation is the final step in medical device manufacturing quality control and it ensures that the manufacturing process is capable of consistently producing devices that meet the quality standards. The process broadly involves the following steps which can also be applied to equipment, tooling and part supply:
3.1 Installation qualification: The manufacturer should verify that the equipment used in the manufacturing process is installed correctly and meets the intended specifications of the manufacturer or supplier.
3.2 Operational qualification: The manufacturer should verify that the equipment operates correctly and consistently and produces devices that meet the quality standards. This will be the bulk of your validation work, as you will be challenging your process. This challenge could be raw material batch changes, different shift patterns, hot or cold factory temperatures or different machine settings.
3.3 Performance qualification: The manufacturer should validate that the manufacturing process consistently produces devices that meet the design specifications and quality standards. At this point you should have tested and challenged your process sufficiently that your performance qualification is performing conformably in the middle of your processing window. If it falls outside, the manufacturer will need to readdress the operational qualification.
3.4 Process monitoring: The manufacturer should monitor the manufacturing process during all stages of the production process to ensure that it remains within the validated parameters and produces devices that meet the quality standards. The more challenge settings you test during the operational qualification stage, the wider (or tighter) your known window for good quality product will be.
Conclusion
Medical device manufacturing quality control is a crucial but complex process that ensures devices meet the highest quality standards and are safe for patient use. By following the design control, production control and process validation steps outlined above, manufacturers can produce high quality medical devices that meet the user’s needs and expectations while maintaining safety and effectiveness.
Meridian Medical is an established and experienced contract medical device manufacturer specialising in a wide range of medical devices. We offer design, regulatory assistance, cleanroom injection moulding, cleanroom assembly, contact packaging and sterilisation management. We have over 30 years’ experience supplying UK and European companies.
To find out more about how Meridian Medical can help you with your medical device manufacture, get in touch today by filling out our online form or contacting us on 01903 732344 or info@meridian-medical.com.
Case study: Supporting in-house production
How Meridian Medical works as an extension of in-house manufacturing operations to extend a customer’s production capacity.
News: Medical device manufacturing and business news
Read insights and articles on issues affecting the manufacture of medical devices, covering an array of topics.