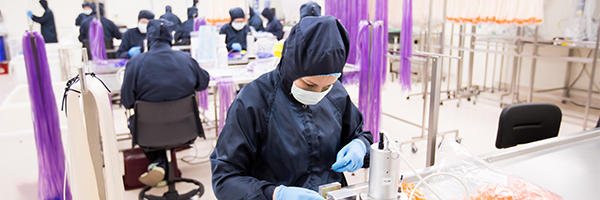
Outsourcing product assembly is a strategic business decision being made by more and more medical device manufacturers, as they seek to better manage manufacturing costs and focus more on innovation.
Faced with a spike in product demand but insufficient production capacity, a global medical technology company made the decision to transfer its medical device product assembly to Meridian Medical.
The company, which partners with organisations around the world to address some of the most challenging global health issues, wanted to outsource some of its ophthalmic procedure kit assembly and it was critical that they chose the right partner.
Ensuring successful product assembly outsourcing
The custom ophthalmic procedure kits included all the required items for use in routine ophthalmic procedures, such as gowns, masks, gloves, cannula, galley pots and syringes. The company approached Meridian Medical with a view to outsourcing the assembly of these kits.
Their quality team visited our site for a facility tour and to carry out a quality audit. Following a successful audit, several of our production team members visited the company’s site for product and quality assurance training.
Meridian Medical quickly started production of the kits, working as an extension of the company’s in-house manufacturing facilities. This was made possible by our ability to easily adapt to the company’s quality procedures. We did this in the following ways:
- The company provided a full kit of parts as if the assembly was to be carried out in their own cleanroom
- The company provided their own assembly procedure and quality documents
- We completed the company’s quality documents and operated according to their procedures
- The kits were assembled and packaged, and delivered to the customer within the agreed lead time.
Generating revenue and improving processes
As part of the outsourcing contract, we produced five types of ophthalmic procedure kit for the company. Our production capacity, and the company’s ability to call on this resource to meet growing demand, helped generate significant additional revenue for the company and gave it the space and flexibility to focus on internal production planning.
At the end of the outsourcing contract, the products, kits, jigs and fixtures used in the assembly process were returned to the company, along with first-offs, test samples and documentation.
Meridian Medical is an established and experienced contract medical equipment manufacturer, specialising in a wide range of medical device design, development and supply services.
To find out more about how Meridian Medical can help you with your medical product design and manufacture, get in touch today by filling out our online form or contacting us on 01903 732344 or info@meridian-medical.com.
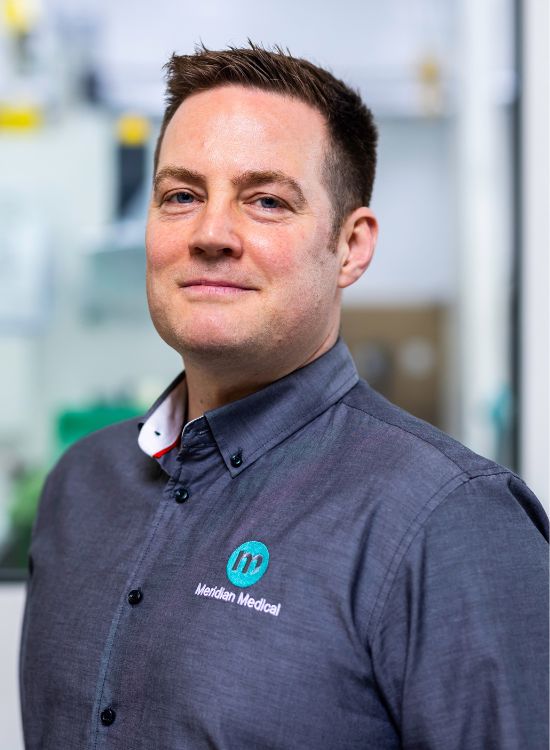
Author: James Fenton, Managing Director
James Fenton, Managing Director of Meridian Medical since 2017, has over 20 years of industry experience. He has been pivotal in developing and producing over 500 types of single-use medical devices, including CE-marked class 2 and 3 devices. With a strong focus on business strategy, project management and customer support, James ensures Meridian Medical's agility and innovation. His expertise is backed by qualifications in Business Studies and Medical Process and Equipment Validation, plus extensive industry training. James's insights into the industry that he has dedicated his entire career to provide a bank of invaluable information aimed at increasing knowledge of and driving advancements in medical device manufacturing.