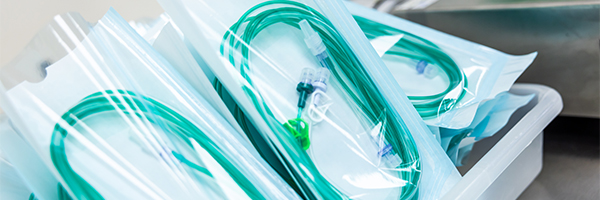
Most would probably consider 2022 to have been the first ‘normal’ business year post-pandemic. Others, including some here at Meridian Medical, would argue that there is no such thing as a normal year any more.
Simply being in business since the pandemic has had its highs and lows, and anyone that is part of the medical industry has also had to deal with its own curve balls.
As a subcontract medical device supplier, Meridian Medical has had the privilege of working with many types of medical device companies, among them manufacturers of critical care devices. Working with these customers means we get to see a fair bit of what influences the industry.
Here’s a look back on the factors that affected medical device manufacturing over the course of this year – they are mentioned in no particular order, just how they come to mind.
Device regulations and notified bodies
Device regulations, including the transition to Medical Device Regulations (MDR), and notified bodies have seemed to be a pain point for every company with medical devices on the market.
After Brexit, the European Medical Device Directive (MDD) split into UKCA, and European MDD, meaning that if you sold to both the UK and Europe, you now need two technical file audits. For most companies this created a fair amount of work.
On top of that, the European MDD then transitioned to MDR, which means that, on recertification or if you were launching a new device, you need to upgrade your files to meet MDR. For older legacy devices or devices with low annual sales, this was particularly challenging, and we saw several customers drop products due to the cost of upgrading the files being prohibitively high.
The transition to MDR caused several other problems in that, as the standard was new, companies didn’t know if they would pass, and if they didn’t, they couldn’t sell products. Changing your certification also requires changing your device labelling and planning your production with stock and label changes.
Of course all of these new certifications, audits and technical file updating cost money. In a year where costs were already spiralling out of control, businesses needed deep pockets to fund all the regulatory changes.
Production demand
2020 and 2021 were tough for medical device companies. As hospitals focused on Covid patients, all other routine surgeries were delayed. This significantly reduced global demand for routinely produced devices.
From Spring 2022 the industry jumped back to life, and we saw significant increases in demand across all of our medical device customers. Many of our customers have had record years and while this is normally great news, meeting that increased demand was very difficult for a number of reasons. Following Covid, lead times for raw materials were pushed out significantly, stocks were low and new orders had to be planned. This made getting more than your normal share of hard work.
On top of that, across the country, staff recruitment and retention were the hardest it had ever been and recruiting good staff needed real finesse. For every business we spoke with, staffing was one of the biggest challenges, but this seems to be easing. Many businesses in the UK had to be quite inventive to get new people on the shop floor and even more creative to keep them happy.
Tyvek supply issues
Tyvek polyethylene fibres are used across many industries. In the medical industry it is mostly used for white oversuits (used in crime scenes, cleanrooms etc), PPE and medical sterilisation pouches.
Due to the extreme weather and flooding in Texas, a significant number of chemical manufacturers were forced to stop production. This, in turn, led to a large number of material manufacturers being unable to get the raw chemicals required for production.
DuPont, which produces Tyvek, had a limited supply of raw materials, with an increase in global demand which led to customers being put on allocation. This led to many medical device packaging companies seeing increased costs and reduced supply for Tyvek packaging.
Coupled with increased demand for supply from the market, it caused serious supply issues.
We’re now somewhere over the hill, but lead times are still long, meaning that careful production planning is required.
Cost of power
Energy costs have affected everyone in the UK, both at work and at home. Many companies in the UK saw significant increases and, while residential energy is price regulated, commercial energy is not.
Many news sources reported on companies facing substantial energy cost increases that made their business unviable. For medical manufacturing, the cost of operating cleanrooms, air filtration and air conditioning, and machinery all increased significantly, and we saw many suppliers’ costs going up, along with the addition of an energy surcharge. The energy crisis, in conjunction with the other factors already mentioned, led to a challenging year for cost.
Silicone supplies
Silicone is used in a variety of medical devices, such as tubing, extrusions, check valves, LSR moulded parts and gaskets. China is the largest global supplier of silicone, followed by Russia.
There are many factors affecting raw silicone supply, but, in brief, China’s silicone production region had power supply issues, which led to a decline in production. This came in tandem with Chinese Covid lockdowns, which caused a decline in output. The second largest manufacturer of silicone, Russia, was no longer able to supply, due to the Ukraine/Russia war sanctions.
Thanks to global demand and reduced supply, market prices increased 25%, with limited supplies. The knock-on effect was quite significant for many industries, especially the medical industry.
The war in Ukraine
The effects of the war in Ukraine isn’t specific to medical manufacturing, but something so significant that it can’t be left out of this review.
Many companies that experienced supply issues during Brexit were quick to get sight of what issues would occur when the war in Ukraine started.
Clearly, there was a huge knock-on effect on the supply of power, with the sanctions imposed on Russia also causing numerous supply chain disruptions. Fortunately, in our area of industry, the effects on the supply chains were low. We did, however, have a number of Ukrainian refugees come to the local area and work with our company.
Looking back at 2022
Despite all the challenges, cost increases, material supply issues and regulatory hurdles, 2022 has been a great year for medical device manufacturing.
For Meridian Medical specifically, we have increased our production team by 30%, have added to our quality and technical teams to handle the increased outputs and taken on a new unit specially to work as a dispatch warehouse.
We have been working with our customers to ensure we can meet their demand and help reduce the impact of these previously mentioned challenges. We will be starting 2023 in great shape, with a fantastic team and look forward to working towards our 2023 goals whatever new challenges the year brings for us.
Meridian Medical is an established and experienced contract medical equipment manufacturer specialising in a wide range of medical device design, development and supply services.
To find out more about how Meridian Medical can help you with your medical product design and manufacture, get in touch today by filling out our online form or contacting us on 01903 732344 or info@meridian-medical.com.
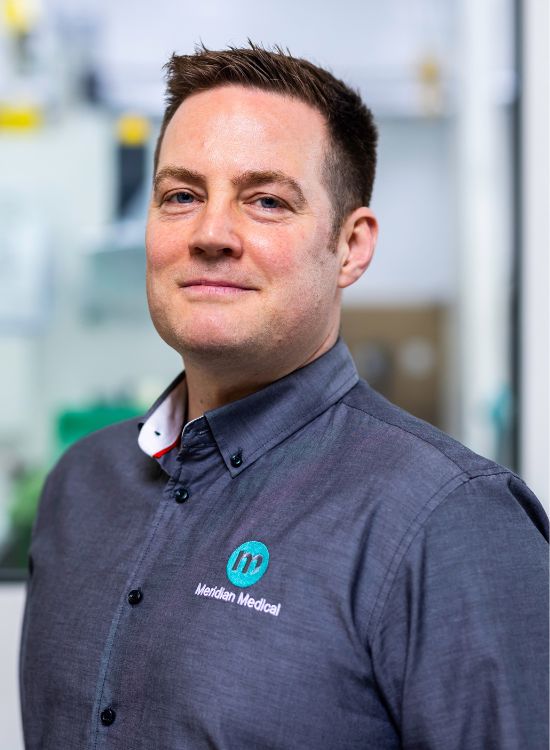
Author: James Fenton, Managing Director
James Fenton, Managing Director of Meridian Medical since 2017, has over 20 years of industry experience. He has been pivotal in developing and producing over 500 types of single-use medical devices, including CE-marked class 2 and 3 devices. With a strong focus on business strategy, project management and customer support, James ensures Meridian Medical's agility and innovation. His expertise is backed by qualifications in Business Studies and Medical Process and Equipment Validation, plus extensive industry training. James's insights into the industry that he has dedicated his entire career to provide a bank of invaluable information aimed at increasing knowledge of and driving advancements in medical device manufacturing.