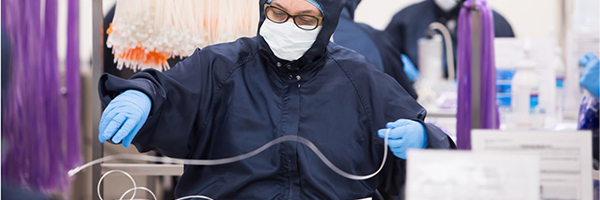
Quality Assurance should not be a unique selling point of a company involved in the manufacture and supply of disposable medical devices. A standard requirement of a company should be that the smallest detail matters. Everything should be perfect.
The challenge to rise to the highest standards is signalled by a commitment to ISO. ISO is the International Organisation for Standardisation. This is a voluntary set of international standards. Since it was established in 1947, the organisation has published more than twenty-two thousand standards covering all aspects of technology and business.
Committing to raise your product to these voluntary standards is the challenge that underpins quality assurance.
What is Quality Assurance?
Quality assurance (QA) is a systematic process of determining whether your product meets the specified requirements. In terms of disposable medical devices, the product should be safe for the end-user and the patient, be effective in its application and offer the level of sterility required for the best outcomes. QA sets and then maintains the necessary standards for the development and supply of products used each day to save lives.
The purpose of QA
There are three clear winners with effective QA: the end-user, the customer and the manufacturer.
The end-user can feel assured that there is a limited chance that the product will fail and will work as intended. The end-user knows that this product is compatible with other accessories and contains exactly what the label claims. If the end-user needs a latex-free product, then this is assured.
Customers want to offer guarantees to the clients, the end-users and have these fulfilled. They want to be free from complaints. They will feel a responsibility to prevent harm and risk to an end-user and look to your QA policy and procedures as the trust they need. QA procedures should meet compliance needs; demonstrate that the product matches the technical file; has passed all testing, and that all claims made are correct.
The importance of QA is best exemplified in the experience of Anaesthetic Medical Systems (AMS). AMS started to see a decline in the quality of the devices being produced by their original supplier. They needed to change how they worked to stem the flow of complaints received. They began a search for a British company with an established reputation for quality.
From the technical team to the development team, Meridian Medical worked to replicate the AMS Sterile A Set range. Using identical materials and specifications, they keep the price of these low margin devices the same. Thanks to the QA demanded at Meridian Medical, AMS has seen a dramatic decline in complaints and are enjoying significant growth in sales across the globe.
Company benefits
It is not just the supply chain that benefits. As a manufacturer, QA procedures ensure there is a repeatable manufacturing process in place that will reduce costs, returns and recalls. With the consistent quality comes an increase in customer confidence and therefore improved business. Ultimately, your QA procedures will ensure your staff receive high-quality training, and that assembly is standardised.
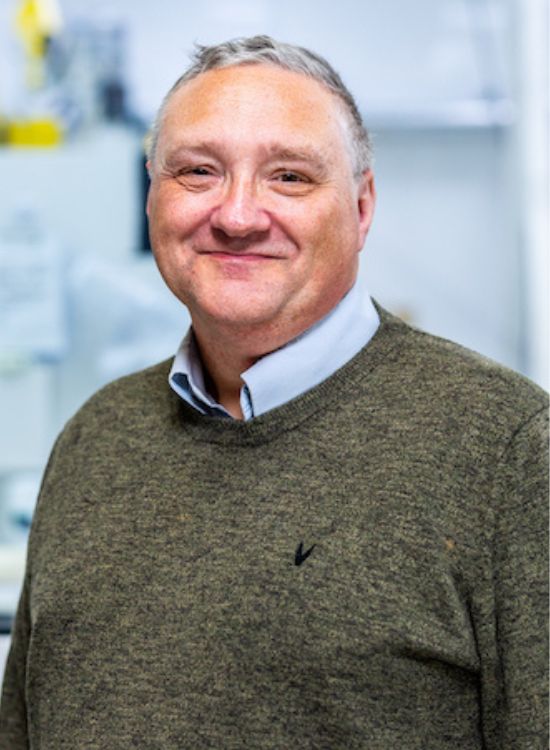
Author: Andrew Wootten, Quality and Regulatory Manager
Andrew Wootten has been at the forefront of Meridian Medical’s quality and regulatory functions for over a decade. With a career in quality management that began in 1989 and extensive experience in the medical device sector since 2002, Andrew is a seasoned expert. He holds a City and Guilds certificate in Quality Assurance, a diploma in Quality Management from BSI, and is a certified internal auditor for ISO 13485, ISO 9001, and ISO 14001. Andrew ensures our regulatory compliance and drives the company’s commitment to excellence in quality and safety, making him a trusted authority in the industry. His deep understanding of global regulatory challenges and unwavering dedication to quality assurance position him as a key figure in delivering safe, compliant and top-quality medical devices.