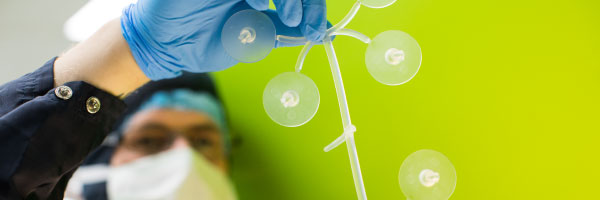
One burning question we often get asked is, “How much does it cost to manufacture a medical device?” In this post, we’ll unravel the intricacies of medical device production costs to provide you with a comprehensive breakdown. Understanding the costs associated with medical device production is useful for industry professionals, especially those in procurement, as it allows you to make more informed decisions, knowing, as you will, why devices cost what they do and which aspects affect that cost the most.
When calculating the intended sale price of a medical device, you need to factor in a number of elements, including research and development costs, fulfilling regulatory requirements, overheads, parts and materials, assembly time, sales and distribution costs, and, ultimately, the desired profit. Together, all of these items significantly influence the overall cost of a finished device. This blog reviews the specifics that influence medical device manufacturing costs in order to help you to understand how those costs are calculated and where costs can be saved.
A Brief Overview of Medical Device Manufacturing
Medical device manufacturing is a meticulous process that involves a significant amount of design, development, testing and production work. The intricacy of this process is essential to guaranteeing the safety and effectiveness of devices that play a vital role in patient care.
Design and development costs can be significant as it’s likely the design process will go through multiple iterations. The designs are then prototyped, tested and refined, with the process repeated until the final design is agreed on and ready to be put into production.
Once the design and development is complete, the device will then be tooled, or set up for mass production. This involves ordering production specification tools, fixtures, assembly aids and any required automation. The assembly process must then be validated and verified to ensure repeatability prior to production beginning. Devices will be subject to quality and regulatory testing, and once completed, approved for sale, before being stored and distributed to the end users.
Factors Influencing Medical Device Manufacturing Costs
There are several factors that influence the cost of manufacturing medical devices and, depending on your device or project, each may affect the price more significantly. The main cost-influencing factors are:
Materials and Components
The choice of materials and components significantly impacts costs, with specialised materials often driving up expenses. Where possible, using off-the-shelf parts and materials saves design and prototyping time, as well as any new tooling that may be required. Typically, materials and components make up around 20-50% of the overall medical device manufacturing costs.
Design and Development
The complexity of the device design and the research and development phase contribute substantially to manufacturing costs. The front-end design costs have to be factored into the overall manufacture or sale cost of the device, as they need to be recouped. These costs are not easy to estimate without knowing the specifics of a project but expect them to be in the high tens of thousands of pounds with prototype products.
Regulatory Compliance
Meeting stringent regulatory standards is non-negotiable, but the work required to gain regulatory compliance adds to your overall medical device manufacturing costs. We recommend that you CE mark your devices in your own company name. It may be tempting and cheaper to have your device supplier CE mark the device on your behalf, however, in the long term it always works out to be a disadvantage. Also, don’t forget to factor in your business ISO registration, auditing and then CE/MDR/Tech file review.
Quality Assurance and Production Validation and Testing
Rigorous testing to ensure your device is safe and effective is another necessary cost in the manufacturing journey. A rigorous and comprehensive validation programme should be conducted to ensure the repeatability of your prediction process, which effectively proves that each device produced is within the required specification. This will involve manufacturing a number of devices and then verifying that those devices are correct, which typically renders them unsuitable for sale. The more complicated your device the larger this cost will be. This task is crucial, as it lays the groundwork for crafting your quality assurance inline inspection plan.
Production Volume
Economies of scale come into play, affecting costs differently for small-scale and large-scale production. In simple terms making 1 is easy and making 100,000 is easy but only making a 100 can be very problematic and costly. The larger the expected volume, the less customised the device becomes and the more the costs above can be amortised into the sale cost. Your buying power also improves as you purchase more of the raw materials.
Sales Costs
Sales and distribution costs involve various elements, including marketing efforts, sales team salaries, distribution channels and logistics. Investing in targeted marketing campaigns to reach healthcare professionals and end-users is essential for driving product awareness and demand. Additionally, maintaining a skilled sales team capable of effectively communicating the value proposition of medical devices is vital for driving sales growth.
Distribution Costs
These encompass the logistical challenges of delivering medical devices to your customers efficiently and reliably, including transportation expenses, warehousing costs and inventory management. Leveraging efficient distribution channels and optimising supply chain operations can help minimise medical device manufacturing costs while ensuring timely delivery to meet customer demand.
Breakdown of Medical Device Manufacturing Costs
In this section we will delve deeper into each of the factors outlined above as influencing the manufacturing costs of medical devices and provide insights into how they contribute to the overall cost.
Meridian Medical has produced more than 1,500 unique medical devices over the past 30 years and quoted even more. The following costs and estimates are best guesses based on our experience of the various projects we have been involved with. There is a huge range of scale between the cheapest and easiest medical device to that of the most complex active devices that can be developed. Keep in mind that Meridian Medical is a specialist supplier of single-use, disposable medical devices when reading the following about factors that influence manufacturing costs.
Materials and Components
Typically, materials and components should make up around 20- 50% of the overall manufacturing cost of the device. For example, this could include polymer, moulded or extruded parts, packaging, labels, cartons or anything else that would be shown on a bill of materials. If outsourcing the design work, then expect to pay a design company £50-£150 per hour depending on the complexity of the project, and then around £500 each for prototyping components, if they are being produced via rapid Service Level Agreement. 3D printed parts will be significantly cheaper, but the materials may not be representative of the finished device.
Processing and Assembly Time
The complexity of the device and the number of parts it features will have a huge impact on your medical device manufacturing costs. Fewer parts that are easy to fit together will always make assembly cheaper than a device featuring lots of parts that are difficult to assemble. Processing and assembly time can again typically make up around 20-50% of the overall cost of manufacturing the device. The processing price is calculated by the hourly rate of assembly, for example, £39 per hour for operator assembly, divided by how many units that operator can produce per hour. Machine hourly rates can differ depending on its size, the expense to run it or its initial purchase price. However, the calculation is the same – hourly rate divided by products produced per hour.
Quality Assurance and In-process Testing
During the assembly process there will inevitably be component scrap or in-process destructive testing, and this will be costed into the finished batch cost. The scrap and testing should always be costed separately to the main production activity, as both should ideally reduce over time and/or reduce as batch sizes increase.
Examples of in-process testing scrap can be:
- Pull testing of joints – for example, at the start of the production batch, five of Item A are bonded to Item B, then pulled apart and the force measured. If the force is above the predestined specification, continue with production.
- Machine set-up materials – an injection moulding machine will require an amount of material before ‘at specification’ production is reached. Price is dependent on the value of the material and the size of the component produced. If your material is £5.00 per kilogram and 3kg is used at start-up, £15.00 has been used before you have any effective product.
- Retained samples and lab test samples – we retain the first and last products out of every batch of product that we produce, as well as two to three samples for lab testing, such as bioburden and EtO residuals. As the batch size increases this percentage cost decreases.
Regulatory Costs
The medical device manufacturing costs involved in gaining regulatory compliance is very specific to the classification of the medical device, depending on whether it is a new device or an updated version of an existing device. Auditing costs should be budgeted at £2,000 per day (per auditor) for your ISO registrations and certification. Device technical file audits can range from £2,500-£8,000 per day depending on whether the audit is remote or onsite. These costs can spiral quickly and should be factored in as recurring costs.
Typical Cost Ranges for Manufacturing Medical Devices
In this section we will look at some examples of typical cost ranges for manufacturing different types of medical devices, including low-complexity devices, moderate-complexity devices and high-complexity devices. These are general estimates and presented as examples only. Actual costs can vary depending on your specific circumstances.
The examples presented below have been created to show how parts and complexity make a difference to overall medical device manufacturing costs.
Example 1: A single component that has been purchased eg. (medical sponge), sealed into a labelled pouch, packaged in boxes of 20 and sterilised by EtO. There are 10 boxes of 20 per shipper.
The device is not inspected or tested in any way and no retained samples are kept. Batch size is 500 units.
Example 2: A single component that has been purchased (eg. medical sponge), dipped in sterile water and then dried. Each sponge is measured to ensure the correct size and weighed to ensure it has been dried sufficiently. As in Example 1, each device is sealed into a labelled pouch, packaged in boxes of 20 and sterilised by EtO. There are 10 boxes of 20 per shipper.
4 x finished products are sent to a lab for EtO residual testing and a single bioburden report. First and last samples are retained. Batch size is 500 units.
Example 3: Three medical sponges (red, green and blue) are dipped in sterile water and then dried. Each sponge is measured to ensure the correct size and weighed to ensure it has been dried sufficiently. At the beginning of each batch, each colour sponge is force tested to ensure uniform durability.
As in Example 1, each device is sealed into a labelled pouch, packaged in boxes of 20 and sterilised by EtO. There are 10 boxes of 20 per shipper. Batch size is 500 units.
Strategies for Cost Optimisation in Medical Device Manufacturing
There are many ways to reduce the average medical device manufacturing cost per unit, but in most cases, to be effective without compromising the quality or changing the specification, they need to be implemented over the lifecycle of the device’s production.
Your first few initial batches will typically be the lowest volume and the batches with the most teething issues. They should also have the highest number of quality control and test samples. As the number of batches increases, you will gather important data that shows the reliability of your process, as well as the outcomes of any external testing. With repeated positive results your testing can be reduced, saving time and money. You may also be able to reduce in-process testing from every device to a random sample or a few every hour. Reducing the testing and inspection based on reliable historic data could save 10% of your medical device manufacturing costs.
As the number of batches increases the process should become more streamlined and production scrap reduced (assuming you have good tooling and a standardised process). The assembly time should also reduce, as the operators become more familiar with the process. This does not always net you a cost reduction, as in most cases production starts slow and ends up in line with the goal assembly time.
Process optimisation can also occur with improved assembly aids, better tooling or automation. These can all have high, upfront costs and, as a result, are not always suitable for your first batches. However, once you have secured regular sales and have a good estimation of expected annual requirements, you may feel more confident in investing further in the process. Effective automation and improvements in tooling could save more than 50% of your medical device manufacturing costs.
Negotiating with suppliers and leveraging economies of scale will also have a huge impact on the manufacturing cost of a medical device. For all the reasons that making the product more often and in larger quantities makes it cheaper for you, the same applies to your suppliers. With effective negotiation, planning and order size increases, you may save around 50% on the materials and components of the device.
Conclusion: understanding the full process reveals where the costs lie
As you have read, there are a significant number of factors to be considered when calculating medical device manufacturing costs. The actual parts and assembly of the device is only one small part of the total manufacturing cost of a medical device. Many of these costs are fixed and do not change even as the number of items manufactured increases. Understanding the estimated annual sales is very important to ensure that all development, manufacturing and sales activities can be paid for.
There is not a single-one-size-fits-all formula for costing and cost optimisation when it comes to manufacturing medical devices, but understanding the whole process can provide insights as to where the costs are and how they can be improved upon.
Having manufactured more than 1,500 different medical devices since we began, Meridian Medical has built up a wealth of knowledge and expertise. Please contact us if you have any questions relating to medical device manufacturing costs, or require any help with any aspects of your medical device production.
To find out more about how Meridian Medical can help you with your medical device manufacture, get in touch today by filling out our online form or contacting us on 01903 732344 or info@meridian-medical.com.
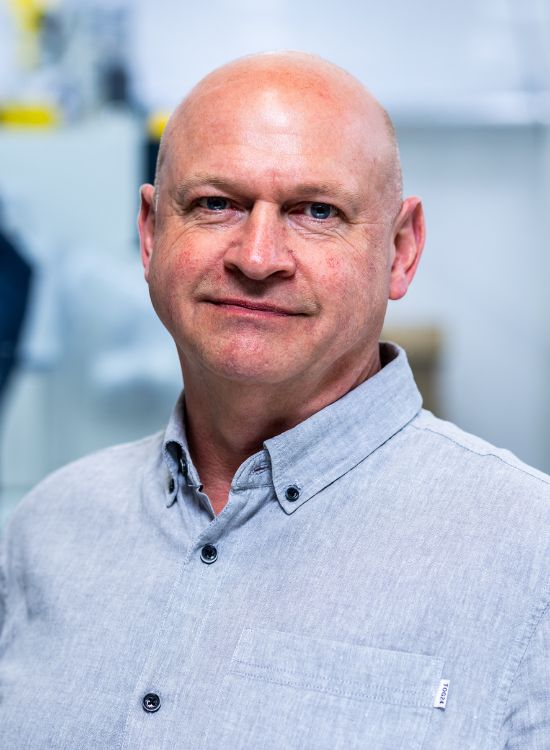
Author: Paul Kearsley,
Technical Manager, Meridian Medical
Paul Kearsley brings a lifetime of engineering expertise to his role as Technical Manager at Meridian Medical. With an HNC in Mechanical Engineering and a foundation built during a four-year engineering apprenticeship, Paul has spent over 40 years running his own design company. Over the decades, he has designed more than 1,000 consumer, industrial, and medical devices, showcasing his ability to deliver innovative solutions across a broad spectrum of industries.
A pioneer in the transition from traditional drafting techniques to modern CAD workflows, Paul began his career on the drawing board, adopted AutoCAD 2D early on, and embraced 3D modelling with SolidWorks in 1997. His vast experience and technical leadership play a key role in Meridian Medical’s commitment to producing high-quality, single-use medical devices.